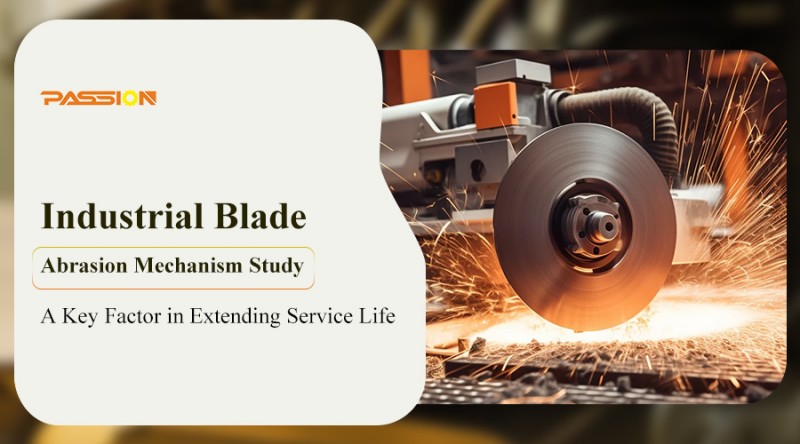
Teollisuuden valmistuksen alalla terien hankaus on aina ollut tärkeä tekijä, joka vaikuttaa tuottavuuteen ja tuotteen laatuun. Tieteen ja tekniikan etenemisen sekä prosessin jatkuvan optimoinnin myötä tutkimusteollisuusteräKulutusmekanismi on tulossa yhä syvällisemmäksi, ja sen tavoitteena on löytää keskeiset tekijät terän käyttöiän pidentämiseksi.

Terän hankaamiseen on olemassa useita syitä, mukaan lukien mekaaninen kuluminen, lämmön kuluminen, kemiallinen kuluminen ja diffuusion kuluminen. Mekaaninen hankaus johtuu pääasiassa työkappaleen materiaalien kovista hiukkasista urien valmistukseen terän pinnalla, ja tällainen hankaus on erityisen ilmeinen, kun leikkaa alhaisella nopeudella. Lämpöhuoli johtuu suuresta määrästä lämpöä, joka on syntynyt leikkuuprosessin aikana, mikä johtaa terän kulutuksen tai lämpöhalkeamien plastisten muodonmuutoksiin. Kemiallinen kuluminen on happea ilmassa korkeissa lämpötiloissa ja terän materiaalin kemiallinen reaktio, matalan kovuusyhdisteiden muodostuminen, siru pois, mikä johtaa terän hankaukseen. Diffuusion kulutus sitä vastoin on, että leikkausprosessin aikana työkappaleen kosketuspinnan kemialliset elementit ja terän hankaus diffundoivat keskenään kiinteässä tilassa, muuttaen terän koostumusrakennetta ja tekee pintakerroksensa haurasta.
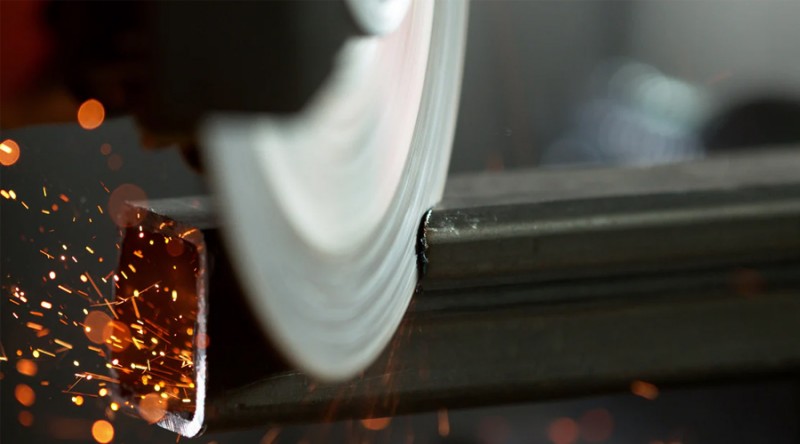
Näiden kulutusmekanismien osalta tutkijat ovat ehdottaneet erilaisia menetelmiä terän kulutuksen käyttöiän pidentämiseksi. Ensinnäkin avain on kohtuullinen terämateriaalien valinta. Käsiteltyjen materiaalien ja leikkausolosuhteiden ominaisuuksien mukaan terän materiaalin valitseminen, jolla on riittävä kovuus, kulumiskestävyys ja sitkeys voivat vähentää tehokkaasti hankausta. Esimerkiksi, kun koneistat vaikeasti leikkaavat materiaalit, joilla on suuri taipumus kovettua, terän materiaali, jolla on voimakas vastus kylmahitsaukselle ja voimakas diffuusiokestävyys, tulisi valita.
Toiseksi terän geometriaparametrien optimointi on myös tärkeä keino pidentää käyttöikäistä. Kohtuullinen terän kulma ja terän muoto voivat vähentää leikkausvoimaa ja lämmön leikkaamista ja vähentää terien hankausta. Esimerkiksi etu- ja takakulmien asianmukainen vähentäminen ja suuremman negatiivisen reunan kaltevuuden käyttö voi vähentää kärjessä olevan reunan kulumista. Samanaikaisesti negatiivisen chamfer- tai reunakaarin hiominen voi myös parantaa terän kärjen voimakkuutta ja estää hakeutumista.
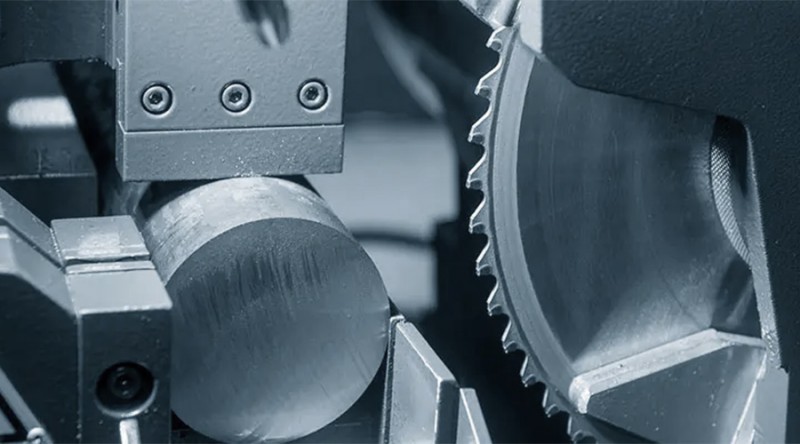
Lisäksi leikkausannon kohtuullinen valinta ja jäähdytysvoiteluaineen käyttö on myös tehokas tapa pidentää terän käyttöikää. Leikkauksen ja rehun syvyys ovat liian suuria, leikkausvoima kasvaa ja terän hankaus kiihtyy. Siksi prosessoinnin tehokkuuden varmistamisessa leikkausmäärä tulisi minimoida. Samanaikaisesti jäähdytysvoiteluaineiden käyttö voi absorboida ja viedä suurimman osan leikkausvyöhykkeen lämmöstä, parantaa lämmön hajoamisolosuhteita, vähentää terän ja työkappaleen leikkauslämpötilaa vähentäen siten terän kulutusta.
Lopuksi oikea toimintamenetelmä ja prosessijärjestelmän jäykkyys ovat myös tekijöitä, joita ei voida sivuuttaa. Leikkausprosessissa terän tulisi yrittää saada terä tai vähemmän kantaa kuorman äkillistä muutosta, jotta terän vältetään epätasaisen voiman ja rikkoutumisen vuoksi. Samanaikaisesti sen varmistamiseksi, että prosessijärjestelmällä on hyvä jäykkyys, vähentävät värähtelyä, voi myös pidentää terän käyttöiän tehokkaasti.
Yhteenvetona voidaan todeta, että keskeiset tekijät teollisuuden inserttien käyttöiän pidentämiseksi sisältävät kohtuullinen terän materiaalien valinta, terän geometriaparametrien optimointi, leikkausannon, jäähdytysvoiteluaineiden käyttö ja oikeat käyttömenetelmät ja prosessijärjestelmän jäykkyys. Terän kulutuksen mekanismin jatkuvan syventämisen myötä tulevaisuudessa uskotaan, että innovatiivisempia tekniikoita ja menetelmiä esiintyy uuden elinvoiman injektoimalla teollisuuden valmistuskentän kehitykseen.
Myöhemmin jatkamme tietojen päivittämistä, ja löydät lisätietoja verkkosivustoltamme (PassionTool.com) -blogista.
Tietysti voit myös kiinnittää huomiota viralliseen sosiaaliseen mediaan:
Viestin aika: marraskuu-15-2024